Optimize Quality with Metal Stamping Cameras for Stamping Inspection

Stamping Inspection: Ensuring Precision and Quality in Metal Stamping
Metal stamping is a critical manufacturing process used across various industries, including automotive, medtech, and electronics. To guarantee the highest level of accuracy and efficiency, stamping inspection plays a vital role in monitoring and maintaining quality. Utilizing advanced optical quality inspection systems, manufacturers can ensure that every stamped component meets stringent industry standards.
The Role of Metal Stamping Cameras in Quality Assurance
A metal stamping camera is an essential component of an optical inspection system, allowing real-time monitoring of production processes. These high-speed cameras are capable of inspecting up to 2,000 test parts per minute. Through integrated vision systems, images of stamped parts are captured and analyzed to detect:
- Dimensional deviations
- Contour inconsistencies
- Surface defects such as scratches, dents, and porosity
By leveraging sophisticated Vision image processing software, manufacturers can automatically evaluate each component, ensuring 100% quality compliance before further processing.
Essential Factors for Accurate Stamping Inspection
1. Lens and Lighting Selection
The precision of metal stamping inspection heavily depends on choosing the right lens and lighting setup. Bi-Telecentric lenses are particularly advantageous as they offer:
- Constant magnification despite object positioning
- High-precision measurement with minimal distortion
- Accurate dimensional evaluation across various depths
Additionally, collimated backlighting enhances contrast, making the contours of stamped parts sharper and more distinct. This improves the accuracy of edge detection and ensures that even the smallest defects are visible.
2. Advanced Image Processing Software
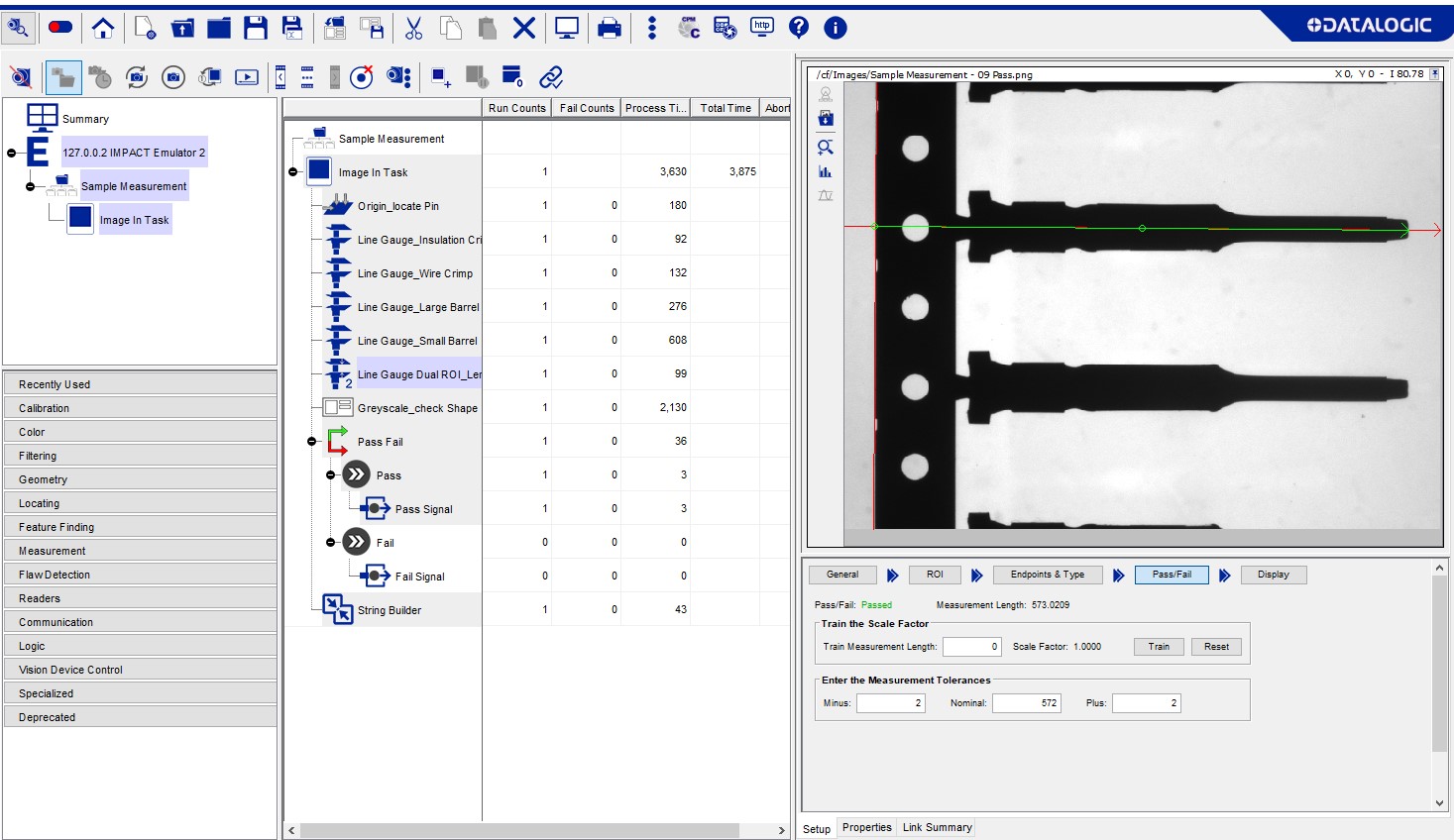
State-of-the-art inspection software, such as Impact Software, incorporates powerful measurement and dimensioning tools based on sub-pixel edge detection algorithms. These capabilities enable:
- Measurement of angles, radii, and diameters with high precision
- Identification of defects at sub-pixel accuracy levels
- Multi-dimensional measurements within a single inspection tool
By implementing sub-pixel algorithms, manufacturers can detect minute discrepancies that traditional pixel-based inspection systems might overlook. This ensures superior accuracy in verifying tolerance acceptability and detecting burrs or plating inconsistencies.
Benefits of Stamping Inspection in Manufacturing
Implementing a comprehensive stamping inspection system offers numerous advantages:
- Enhanced Quality Control: 100% inspection ensures no defective parts proceed to secondary processing.
- Reduced Material Waste: Early defect detection prevents adding value to substandard materials.
- Increased Production Efficiency: Automated systems minimize the need for manual inspections, speeding up production.
- Cost Savings: Identifying defects early reduces the likelihood of costly rework or product recalls.
In today’s fast-paced manufacturing environment, stamping inspection is an indispensable process for ensuring the highest quality standards. With cutting-edge metal stamping cameras, bi-telecentric lenses, collimated lighting, and advanced image processing software, manufacturers can achieve superior precision, minimize waste, and maximize production efficiency. Investing in robust stamping inspection technology ultimately leads to higher customer satisfaction and a competitive edge in the market.
For more information about our machine vision camera solutions or for customized advice, please contact our sales team. Our experts are ready to assist you in integrating these advanced systems into your production processes.
Back